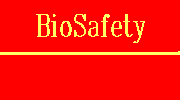
|
BioSafety Journal
Pontificia Universidad Católica de Valparaíso
ISSN: 1366 0233
Vol. 1, Num. 1, 1995
|
BioSafety
Volume 1, Paper 3 (BY95003), May 5th 1995
Online Journal, URL - http://bioline.bdt.org.br/by
Appraisal of the practical effectiveness of biosafety
controls in biotechnology with special reference to safety
cabinets
Ray P. Clark
Thermal Biology Research Unit, Kings College London, Campden
Hill Road, London W8 7AH
Ray@medi.demon.co.uk
Code Number: BY95003
Size of Files:
Text: 17K
Graphics: No associated graphics files
SUMMARY
This paper describes the development of microbiological safety
cabinets for the safe handling of potentially hazardous
material. The test methods required to establish their
performance are discussed. It is suggested that a similar
approach based on Operator Protection Factors could be
adopted for other equipment used for biotechnology.
INTRODUCTION
There is world wide awareness of the need to control the
generation and spread of potentially hazardous biological
aerosols both in research laboratories and in manufacturing
facilities. Arising from this is the need for containment
systems and for methodology which can validate their
effectiveness in protecting the safety of people and the
environment.
Many countries now have legislation which requires that risk
assessment be undertaken for work involving potentially
hazardous material and that, where appropriate, control
measures be provided to prevent exposure to potentially
hazardous organisms or toxic material. For example, in the UK,
there are the COSHH (Control of Substances Hazardous to
Health) Regulations which were introduced in 1988 (4).
These provide a framework for the assessment of hazard in
relation to appropriate control measures, and back up the
requirements of the 1974 Health and Safety at Work Act
(1). These COSHH regulations are used to implement the
requirements of the EC Directive 90/679/EEC on the
protection of workers from biological agents (6).
HISTORICAL PERSPECTIVE
Current concepts for the safe handling of microorganisms date
back just over 20 years and, in the UK, were given impetus
from the escape of smallpox virus in 1973 and 1978 from
laboratories in London and Birmingham. In 1975 a working party
set up as a result of the first smallpox outbreak, produced a
framework and code of practice for handling potentially
pathogenic organisms. Subsequently, there was great interest
in improving laboratory safety by developing safe working
methods and designing equipment which was suitable for
handling pathogenic organisms.
MICROBIOLOGICAL SAFETY CABINETS
In the 1950s the Public Health Laboratory Service (PHLS) in
the UK had recognised that special facilities were required to
handle pathogenic organisms. This recognition resulted in the
design of a Class I microbiological safety cabinet
which has remained relatively unchanged in concept to the
present day. The Class I safety cabinet is basically an
enclosure with air flow from the laboratory, through the front
aperture and over the work away from the operator, with the
discharge air being filtered. This cabinet was designed
specifically, and only, to protect the operator from exposure
to any bioaerosols generated within the working area. However,
as cell culture techniques became more widely used, there was
not only a need to protect the operator from exposure to
bioaerosols but also a requirement to protect the work from
contamination from any organisms in the general laboratory
air. The Class II safety cabinet was developed which
enabled both operator and product protection to be available
in an open fronted cabinet. Such cabinets became increasingly
popular and are now the main kind used in biological research.
For situations where a more rigorous barrier was required
between the work and worker, the Class III safety
cabinet was developed. This is sometimes called a glove box
and the operator works through gloves mechanically attached to
the cabinet which itself is maintained at negative pressure by
a flow of air which is filtered as it enters and leaves the
cabinet. Glove boxes were also extensively used in the nuclear
industry and sophisticated designs evolved. Test methods for
glove boxes were also developed and the technology became well
developed. Thus, during the late 1970s microbiological safety
cabinets in three classes (I, II and III) were becoming
established and widely used.
STANDARDISATION
In some institutions specially designed facilities were built
specifically to handle highly pathogenic organisms such as
smallpox and there were regular and rigorous checks of the
filters and seals and glove systems to ensure their integrity.
However, in hospitals, research institutes and universities
many safety cabinets were used with little regard to the real
effectiveness of the systems. Problems of performance were
much more common with cabinets having an open front and
relying for their containment on an air curtain at the front
aperture. Although open fronted safety cabinets came into
widespread use in the mid 1970s there were very few methods
available to test their effectiveness.
There was clearly a need for standardisation of some kind and
in 1976 the National Sanitation Foundation of America
published NSF 49 which specified tests for filters
and seals and also described a test to evaluate the
effectiveness of the air curtain at the front of Class
II cabinets. This standard was followed in 1979 by the
publication of British Standard 5726 (3) which,
introduced the concept of a quantifiable " Operator
Protection Factor". The protection factor concept is due
to Dr. Owen Lidwell (9) who chaired the British Standards
Institute committee which published the 1979 safety
cabinet document.
It was recognised that the containment performance of safety
cabinets could not be defined simply by air velocity;
effective containment was a function of air velocity,
turbulence, internal geometry and aerodynamics as well as
external influences in the immediate environment, such as the
movement of people and doors, proximity of ventilation ducts
etc. It was realised that the only realistic way to test for
the level of containment was to mimic a work situation where
aerosol was released inside the cabinet and to identify and
measure that which escaped from the cabinet. Here the Operator
Protection Factor proved to be of real value.
The original way of measuring operator protection was to
release an aqueous bacterial aerosol within the safety cabinet
and to use strategically placed bacterial samplers in front of
the working aperture to quantify escape of organisms. The
Operator Protection Factor numerically describes the
results of such tests in a way that relates the exposure
resulting from the escape of hazardous aerosol from the
cabinet to the exposure that a worker would experience if the
work was carried out on the open bench. It specifies the
results of tests in a non dimensional way which does not rely
on any particular test method. It can be applied to tests
other than microbiological, as long as the test system meets
various criteria concerned with aerosol generation, sampling
and identification.
The 1979 version of BS 5726 (3) required manufacturers
to submit examples of Class I and II safety
cabinets for validation tests to show that they achieved
Operator Protection Factors in excess of 10^5. This
rapidly brought about improvements in the cabinets available.
However, it became apparent that although a particular safety
cabinet may have passed the validation test, this did not
guarantee that others in a production run would perform in
exactly the same way. Subtle variation of manufacturing
technique or tolerances, of fan and filter specifications and
of the environment in which the cabinet was put, could
dominate performance.
It therefore became important to test individual cabinet
installations at commissioning and subsequently at routine
maintenance periods. Clearly it was not desirable that these
on-site tests used a challenge aerosol of microorganisms, such
as Bacillus subtilis spores or pigmented cells of
Serratia marcessens, which were commonly used
initially. Use of these could cause gross contamination of
cabinets and laboratories (some 10^8 cells would be released
in a single test) and there was also a potential health
hazard. Serratia marcessens is a low grade pathogen
(Ref) and has been responsible for bacteraemic infections,
while some individuals are allergic to B. subtilis. For
all of these reasons the use of microbiological tests was, and
is, restricted.
To meet the new need for an in-situ test the potassium
iodide KI Discus system was developed (8) which enabled
on-site measurements of containment to be made whenever safety
cabinets were commissioned and maintained. This system
produced a standard aerosol from an aqueous solution of
potassium iodide (8).
In the period between 1979-1992 the concept of measuring
Operator Protection Factor at the work place became
widely accepted and the subject of regulatory requirements in
the UK and elsewhere. In consequence, the latest version of
BS 5726, published in 1992 (7), now specifies in
considerable detail the KI test system and how it is to be
used for validation, commissioning and maintenance tests.
WIDER USE OF CONTAINMENT TESTS BASED ON THE OPERATOR
PROTECTION FACTOR
During the period of the development of tests for safety
cabinets, the same tests were frequently applied to laboratory
fume cupboards and to other local exhaust ventilation systems
where operator protection needed to quantified. Such
measurement techniques were, and are still, in advance of
tests for containment or leakage from fume cupboards which are
based on trace gas analysis. (5)
The application of the concept of Operator Protection
Factor and its measurement using potassium iodide was
extended to the containment measurement of complete
laboratories or suites of laboratories. If a potassium iodide
aerosol is liberated within a room then aerosol that escapes
into the surrounding areas can be measured and it is possible
to define an Operator Protection Factor between the
room and the surroundings.
There is considerable merit in considering a single, unifying
philosophy and methodology for containment measurement over a
wide range of open fronted local exhaust ventilation systems
(safety cabinet, fume cupboards, local hood ventilation
systems, carcinogen and radio pharmaceutical safety cabinets).
The concept would seem to be of potential value in quantifying
containment in large scale biotechnology plant.
ARE CURRENT CONTAINMENT TESTS ADEQUATE ?
For open fronted safety cabinets used for handling potentially
pathogenic organisms, the fact that some of a test aerosol
escapes from the safety cabinet working area into the
laboratory, demonstrates that the containment of such cabinets
is not infinite; nevertheless, the requirement that the
Operator Protection Factor should be greater than 10^5
has proved to be a realistic value for high protection.
However, the process contemplated may require a greater level
of containment than is possible from a safety cabinet.
Complete containment in cases where any contact of operators
with organisms is undesirable will require the segregation of
the worker from the work with all of the operational
difficulties that this entails.
An important point about the use of the containment test is
that it can instantly identify those cabinets which perform
badly due to design or installation/operation fault or because
of a poor environment.
APPLICATION OF SAFETY CABINET CONCEPTS
From an equipment and testing standpoint, safety cabinet
evolution and the development of Operator Protection
Factor tests is very much a success story. The methodology
is now well established and is now spilling over into other
areas of science where containment is important (such as fume
cupboards etc.). Another important principle and one reason
why safety cabinet standardisation work has been so successful
is that the definition of performance criteria does not take
into account the potential hazard of the materials that are to
be used in the cabinet. The criterion is the performance of
the cabinet. British Standard 5726 (7) gives guidance
on construction and testing procedures whereby a cabinet can
perform to a consistent, measurable, and sustainable level.
The methods of test give easy comparison between individual
cabinets at different times and between different cabinets and
allows then to be used with confidence to provide the defined
level of protection.
Protection of the worker requires risk assessment. The value
of the Operator Protection Factor is that it allows
risk assessment to be carried out on the basis of reliable
quantitative information. It is only when this is available
that an objective risk assessment can be made as to whether
the performance of the cabinet is satisfactory for the work
proposed having due regard to the pathogenicity of the
organisms involved.
Such an approach, which defines performance and allows any
legitimate and justifiable method of defining it, allows
different, and possibly innovative, methods of achieving a
given and specified level of performance.
BIOTECHNOLOGY STANDARDISATION
Can the principles and methods adopted for safety cabinet
standardisation be applied for other equipment where there is
a need to protect operators, workers and the environment from
exposure to organisms leaking from equipment and processes ?
This question is particularly important in relation the CEN
Standards initiative for Biotechnology which aims to produce
55 standards in the whole field of biotechnology and, in
particular, 21 standards for the performance of individual
types of equipment.
The standards for performance criteria will not, except in
specific cases, address questions of product quality, since
there are many standards and codes of practice already dealing
with this. They will be concerned with criteria for protecting
workers and the environment from any organisms which may be
potentially hazardous. The concept of defining the performance
and then, separately, deciding whether performance of the
equipment with a given level of performance is adequate to
control the risks inherent in a particular process, seems to
be generally appropriate for standardisation of biotechnology
equipment. In many cases the difficulty experienced initially
with safety cabinets - that there are inadequate testing
methods - will apply to other items of equipment and create
the need for research to develop such methods.
REFERENCES
1 Anon., 1974. The Health and Safety at Work Act, HMSO_ISB No
2 10 543774.
2 Anon., 1976. US National Sanitation Foundation Standard
No.49, Class II (Laminar-flow) Biohazard Cabinetry.
3 Anon., 1979. British Standard BS 5726, British Standards
Institution, Linford Wood, Milton Keynes, MK14, 6LE, UK.
4 Anon., 1988. The Control of Substances Hazardous to Health
Regulations (HMSO-ISBN 0 11 086757 1 and Approved Codes of
Practice (HMSO-ISBN 0 11 885468 2).
5 Anon., 1990. British Standard BS 7258: Laboratory Fume
Cupboards, British Standards Institution, Linford Wood, Milton
Keynes, MK14, 6LE, UK.
6 Anon., 1990. 90/679/EEC, Council Directive on the
protection of workers from risks related to exposure to
biological agents at work, Official Journal of the European
Community, L31, 33 (374) 1-12.
7 Anon., 1992. British Standard BS 5726, 1992. British
Standards Institution, Linford Wood, Milton Keynes, MK14, 6LE,
UK
Part 1, 1992. Specification for design, construction and
performance prior to installation, 20 pages.
Part 3, 1992. Specification for performance after
installation, 8 pages.
8 Clark, R.P and Goff, M.R. 1981. The potassium iodide test
system for open-fronted microbiological safety cabinets.
Journal of Applied Bacteriology, 51 439-460.
9 Lidwell, O.M., 1960. The evaluation of Ventilation, Journal
of Hygiene, Cambridge, 58, 297-305.
Published by Bioline Publications Ltd and Science and
Technology Letters.
Copyright held by the author.
Editorial Office: biosafe@biostrat.demon.co.uk
|